METALLURGICAL LABORATORY
Mueller’s Metallurgical Laboratory located at its Port Huron, Michigan campus primarily works with its industrial metals business units within Michigan. But it also supports the entire Mueller Industries family when called upon. With over a century of combined metallurgical experience, along with the most advanced technology available for our industry, Mueller can continue to ensure our customers receive the quality product they have come to expect. Below is an explanation of some of the areas of testing and technology in use at Mueller.
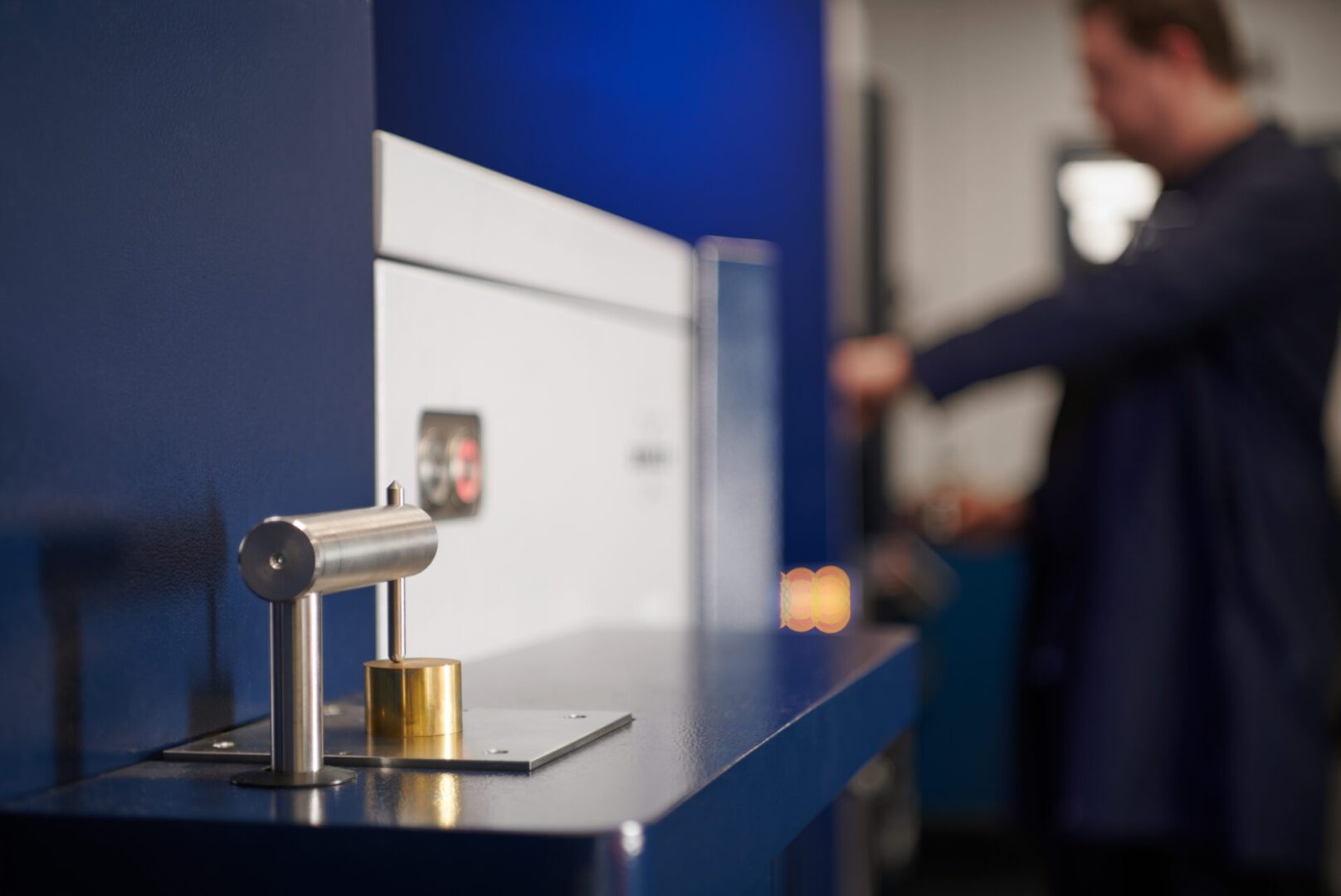
Physical Analysis
Tensile strength, yield strength, and elongation are mechanical properties typically called out in customer and/ or industry specifications for finished products. These material properties are critical in understating how the material will react to various stresses and applications. Included is an image of one of the two state-of-the-art tensile testers used in Mueller’s laboratory to determine these mechanical properties.
Elongation Testing – This method is used to measure a material’s ductility and strength by stretching it until it breaks and measuring how much it stretches without returning to its original shape. The test is performed on brass to determine its elongation at break, which is the amount of plastic deformation it experiences.
Rockwell B Hardness – A standard industry method for testing the hardness of brass, this test utilizes a Rockwell hardness testing machine with a tungsten carbide ball indenter that has a load range from 15kgf to 150kgf. Our machine applies a known load to the indenter causing a depression in the brass. Rockwell B Hardness values are considered a mechanical property commonly called out in customer or industry specifications for finished products. It is a valuable indicator of a materials ability to resist impact and its ductility. The test provides information about a material’s tensile strength, wear resistance, and ductility.
Brinell Hardness Test – Brinell and Vickers are also different types of hardness values used for aluminum and micro-hardness testing respectively. Primarily used for aluminum forging produced by Mueller Brass Forgings, our Brinell Hardness test uses a carbide ball indenter having a load range from 1 to 3000kgf.
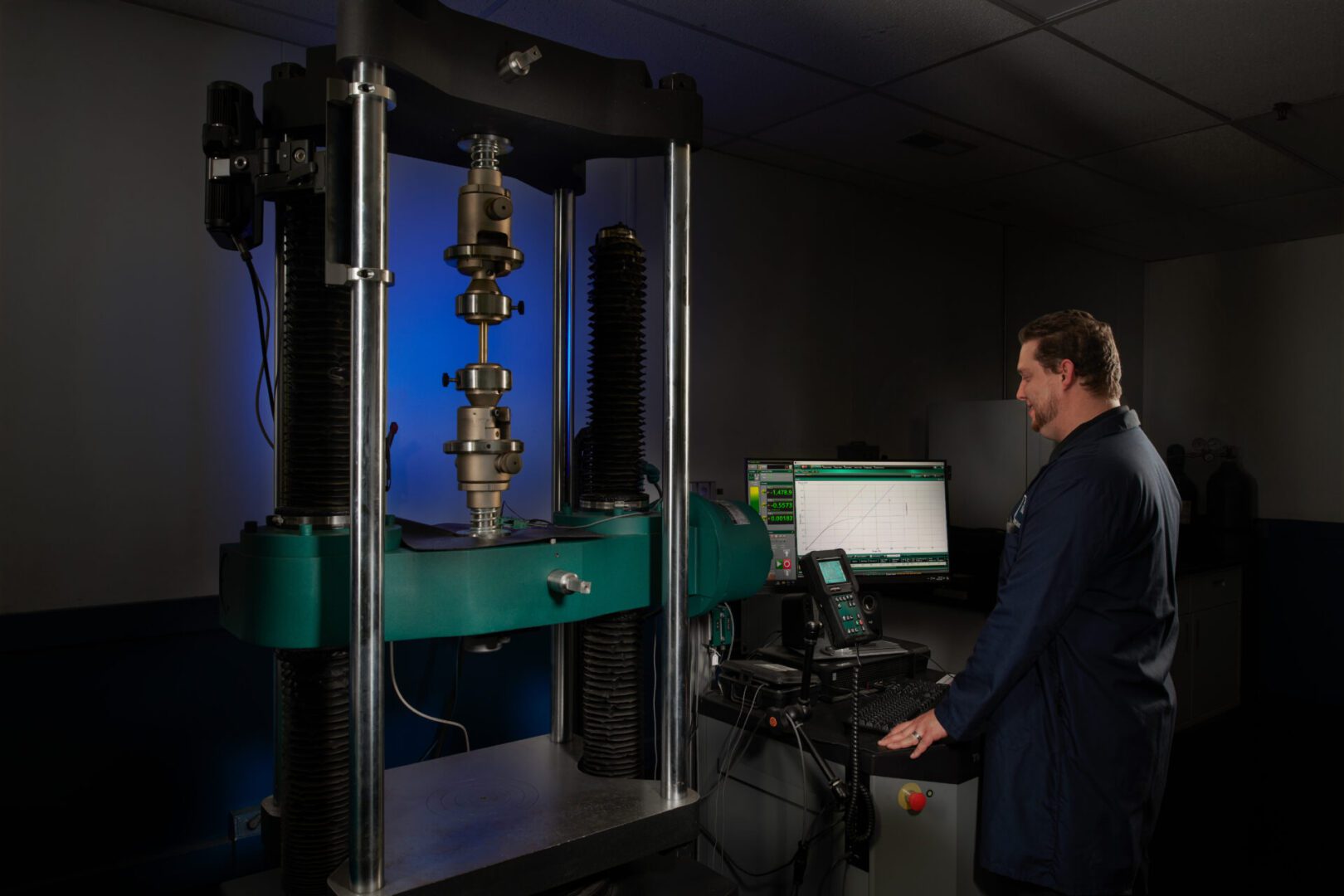
Chemical Analysis
Chemical analysis is performed frequently during and after production or our brass rod alloys to ensure they meet customer, regulatory, and Mueller standards. Optical Emission Spectroscopy (OES) and X-Ray Fluorescent (XRF) Spectroscopy are both utilized to ensure accurate and precise determination of the brass rod. OES and XRF are two different instrumental ways of determining a materials chemistry.
The strength of OES is that it is better suited for analyzing lighter materials such as Aluminum, Silicon and Phosphorus for example. It also has the advantage of being able to analyze small and odd shaped materials such as a customer’s part. The strength of XRF is that it is more accurate when analyzing heavier elements such as copper, zinc and lead which are the major components of brass. Mueller Brass Co. uses both types of technologies to give our customers the best of both worlds.
Optical Emission Spectroscopy (OES) - OES relies on optical aspects of a sample. The way a sample reacts to the testing proves the basis for the results, which are based on known information about the different compounds and elements. An optical emissions spectrometer applies electrical energy to analyze the alloy or metal’s composition. The benefit of this tool is that it can initially review any impurities found in the metal.
X-Ray Fluorescence Spectroscopy (XRF) – The XRF technique creates a main X-ray beam to excite fluorescent radiation from a sample. The XRF spectrometer ionizes the atoms, which then release photons. As the sample emits radiation from the X-ray beam, the technician uses a spectrum to determine the composition of the sample. Our laboratory uses this method to get an exact measurement of chemical compositions in samples. X-ray Spectroscopy is a valuable tool utilized to analyze the chemistry of our brass rod alloys both during and after production. This piece of state-of-the-art equipment helps ensure that very alloy is produced to its correct specification and chemistry.
Metallurgical Analysis
Sometimes it is necessary to look beyond the chemistry and mechanical properties of the material to ensure a quality product for our customers. This involves examining the internal structure of the metal. For this purpose, we use a number of microscopic technologies. Images of two of these instruments are shown below.
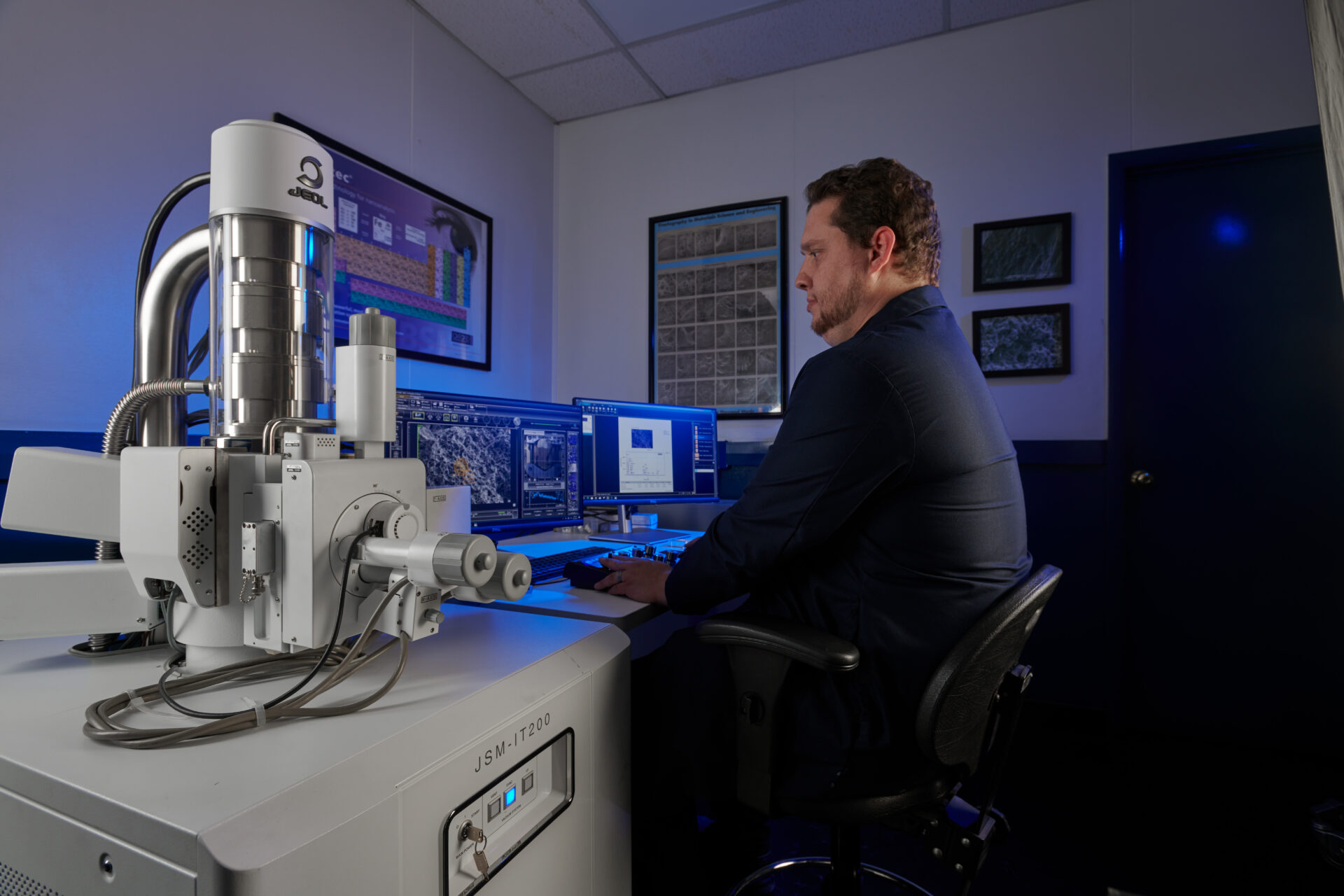
A Digital Microscope and Optical Microscope are instruments capable of examining the internal structure of the metal after it has been polished and etched. For example, this equipment allows for the review of grain size, lead distribution, and metal phase distribution. All these constituents can affect the performance of the finished material.
Mueller also has a Scanning Electron Microscope (SEM) with an Energy Dispersive Spectrometer (EDS) attached. The SEM uses a highly focused beam of electrons to provide greater magnification and resolution compared to microscopic technologies that use light. This results in more information about the morphology and topography of sample being examined.
The EDS allows for the chemical analysis of very small areas made visible by the SEM. This provides the ability for identification of these areas based on chemical spectra data. These two functions used in conjunction provide advanced capability for analyzing surface issues, fracture-related failures, and microstructures in metal-based materials.
Wet Lab
Wet–Chemical Analysis - Our M.E.T Lab will utilize our Wet Lab if necessary to verify chemical compositions of samples. The laboratory will comply with testing standards set by the Metallurgical Testing Board, which states that this testing is “final determination” in a sample’s composition.
Scrap Sample Testing – Along with testing production samples, the M.E.T Lab will test incoming scrap to verify the chemical compositions. This will ensure that Mueller Brass Co. is not cross-contaminating our scrap stream with unwanted chemicals.
Incoming Scrap Analysis
Incoming scrap analysis is an important step to prevent contamination of finished products. Certain elements are not compatible with all alloys and needs to be segregated. This is critical to ensure each alloy family meets regulatory and customer specifications. Frequent chemical analysis is conducted on incoming scrap to prevent this type of contamination.
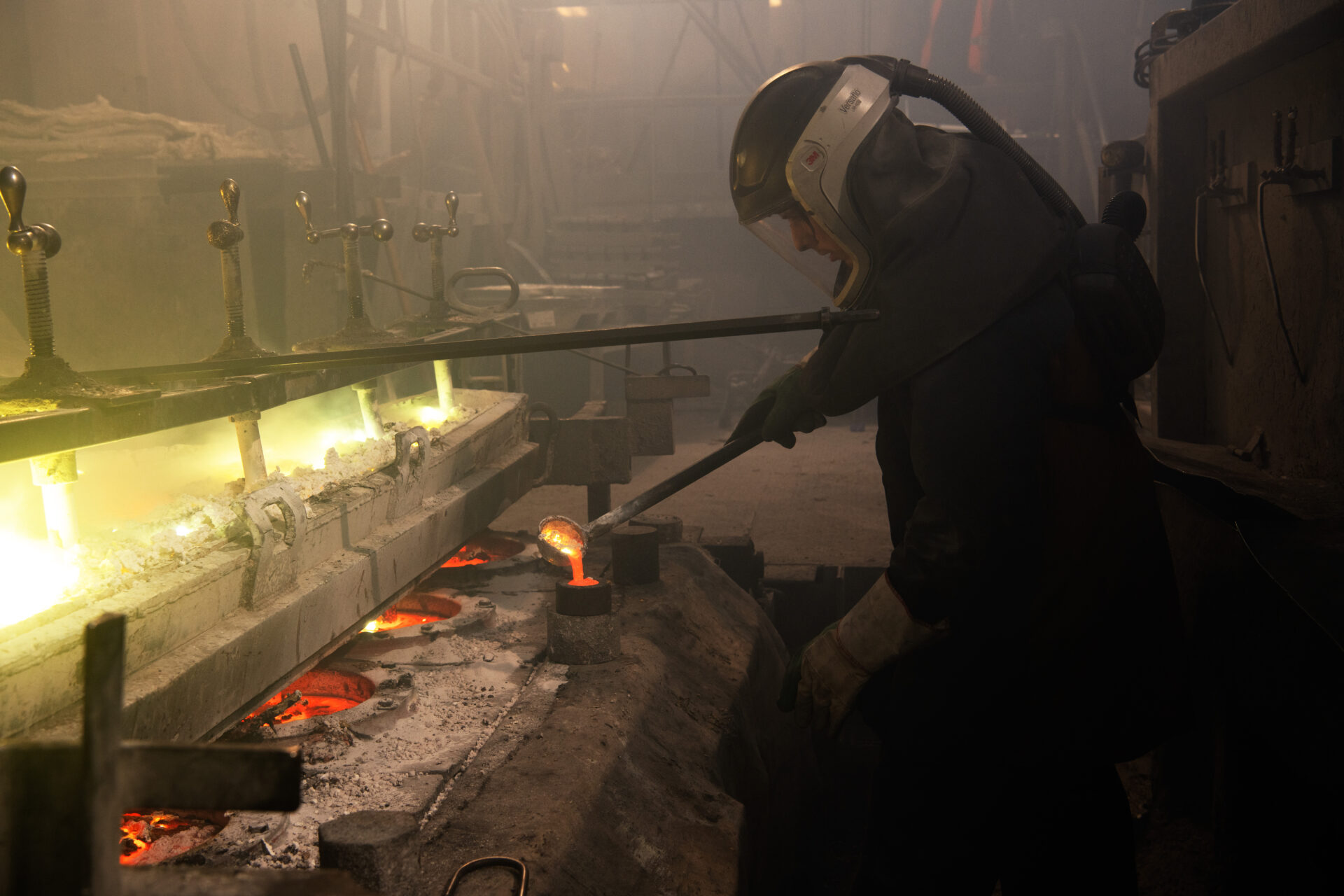
Certifications – ISO 9001 & IATF 16949
To ensure Mueller Brass Co.’s laboratory performs to the highest standard of quality, the laboratory is certified to both ISO 9001 and IATF 16949, independently from the Rod Mill plant.
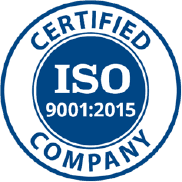
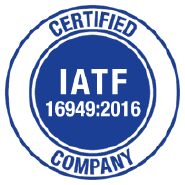